THE HISTORY OF BUR ROOF SYSTEMS
Built-Up Roofing, or BUR for short, first appeared around the mid 1800’s. It is a roofing system where multiple layers of asphalt get applied between ply sheets (or felts) over the roof deck and insulation.
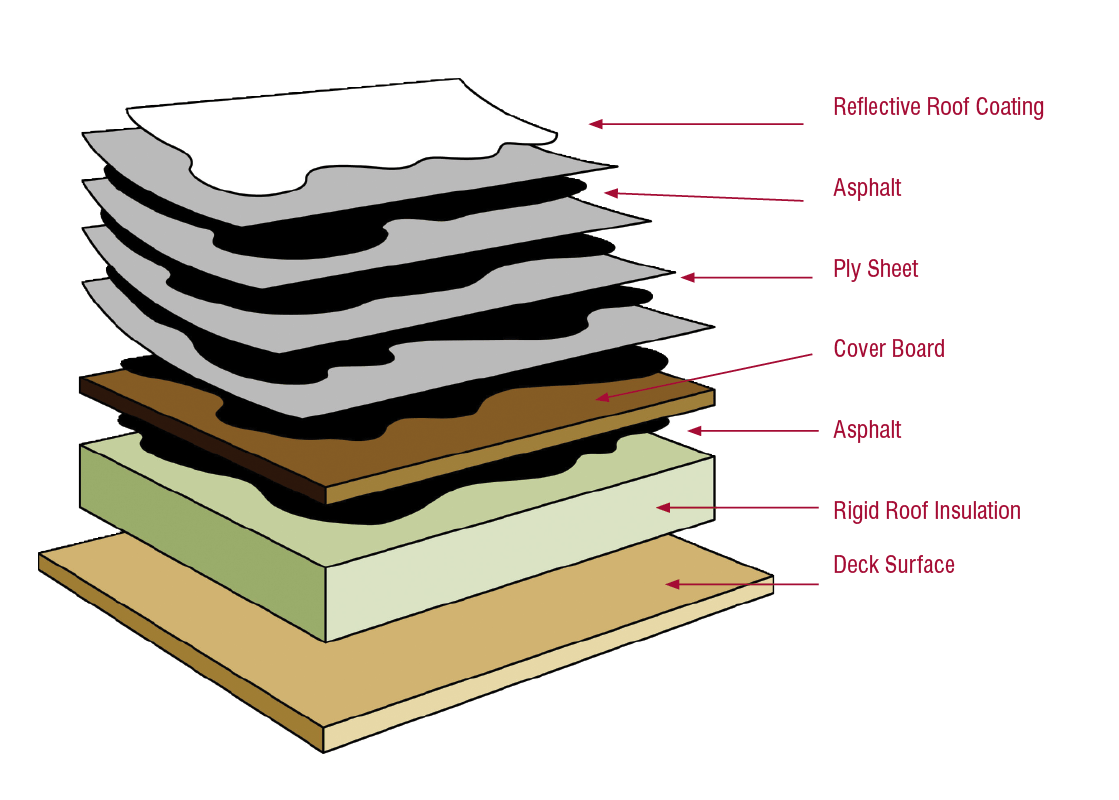
BUR systems are very effective in many different geographic areas and climates.
Historically, BUR roofs were the first “flat” roofs to be used in construction. The familiar image of a man with a mop spreading black tar onto a roof invokes a certain nostalgia among the roofing community. If that roofer were to mop the hot tar onto a sloping surface, the fluid tar would simply fall down the slope with gravity. Therefore, the only place a BUR roof could be installed was and is on a flat surface. Eventually, the technology of the material evolved from “tar” to “refined asphalts” and from “paper” to “felt” – and the performance of BUR systems improved greatly.
WHAT ARE THE CHALLENGES OF A BUR MEMBRANE SYSTEM?
Premature breakdown due to flat or low slope
When rain and/or snow falls on a roof or dew accumulates, it needs proper drainage to naturally get removed from the roof surface. If a “flat” roof is truly flat (and therefore has zero slope and improper drainage), that water will only get removed either through evaporation or absorption into the roof. Either way, it sits on the roof much longer than it should, leading to premature roof failure and increased chance of leaks into the building.
Ponding Area
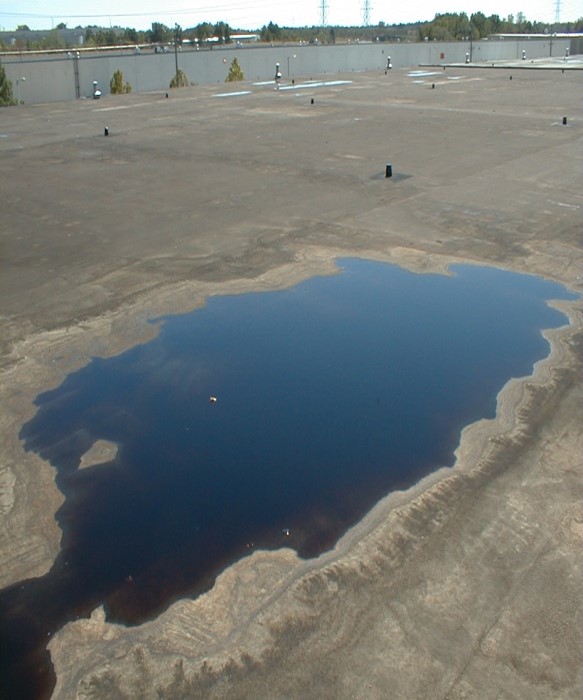
A Ponding Area can be defined as any location on a roof where water remains longer than 48 hours. A Ponding Area of water 1” tall, covering a 10’ x 10’ area, weighs 520lbs. (See Quick Reference: Weight of Water per Inch for Ponding Water — Roof Online).This increased weight can cause a roof to sag. As it begins to sag, it creates a depression lower than the surrounding area, further exacerbating the future potential ponding at that location. Any accumulated roof moisture will follow gravity naturally to these areas and bring along dirt and contaminants, further filling the depression, condensing and retaining moisture longer. It is a vicious cycle. The longer these areas remain in this ponded state, the faster the areas break down - and ultimately fail. Water evaporates at different rates, with higher temperatures accelerating the process. As a rule of thumb, a stagnant pool would average ¼” of water evaporation per day.
Air Conditioning Equipment
HVAC equipment is commonly located on top of the flat roof surface, and the equipment itself, as well as the normal operational processes of the equipment can contribute to roof surface issues.
Weight of the AC unit itself will “Point Load” the roof where it is located, and that weight can begin to stretch or depress the roof surface, creating a ponding area.
Process of conditioning air
HVAC roof top equipment intakes the outside air, filters it, and changes its temperature before supplying it throughout the building. A bi-product of conditioning the air is condensation vapor, which accumulates as water and must be removed from the HVAC equipment. Almost all HVAC equipment uses a form of condensation pipe to provide a path for this water bi-product to drain from the unit to and off the roof.
A very common roof issue occurs when the condensation pipes are not secured properly to the drain, causing leaking around the HVAC rooftop equipment. The continuous flow of water will not allow for it to properly evaporate. This water will end up in a ponding area, and without the ability to evaporate, it will ultimately result in infiltration into the building or insulation through surface break down.
Penetrations and Vent Pipes – Climatized buildings have various rooms and functions being performed inside the building. For proper building health, ventilation from the building may be needed in bathrooms, kitchens, attic spaces, and other areas. When buildings have multiple rooms, the roof can have multiple penetrations (or breaks in the roofing material) coming through its surface.
Because the penetrations (such as vent pipes) are made of metal, and the Gravel BUR roof if made of asphalt layers (as discussed above), temperature can cause cracking around those areas. As the metal expands and contracts at a different rate than the asphalt when under temperature, cracking can occur at those locations. If not monitored and treated, the seal around those joints will open and cause water leakage into the building.
HOW DO I PROTECT MY BUR MEMBRANE SYSTEM?
From ponding areas: Clean off all the accumulated dirt and contaminants from those areas. Once the area is properly cleaned and dried, different materials can be applied to resist surface breakdown in ponding areas. Examples of such suitable Karnak materials include: 19 Ultra rubberized asphalt cement, 502 SEBS mastics and roof coating, 229 SBS rubber reinforced asphalt, and 670 silicone coating.
From leaking HVAC Equipment: Leaking HVAC equipment is a building owner maintenance issue and is not covered in most roofing material manufacturers warranties. Water remaining on the roof surface after 48 hours is considered a ponding area and should be considered a maintenance item.
From penetrations: At roof penetrations like drains, vents, and rooftop equipment, roof materials typically split and crack faster than the field of the roof. Different construction materials react differently to hot/cold temperatures and will expand and contract at different rates. That differential of movement separates the connection points, but most of the time can be easily resealed during scheduled maintenance and cleaning. Only when it goes unchecked for long periods of time does it require more drastic measures. Examples of suitable Karnak materials include 19 Ultra rubberized asphalt cement, KarnaFlex SEBS Mastic, and 229 SBS Rubber Reinforced Asphalt Mastic.
Conclusion
Overall, a built-up roof is a popular option for architects and building owners for its durability, widespread adoption by many roofers, and ease of application. From the many roof substrates to choose from, built-up roofing should be on your short list.
__
By John Doan
Karnak – West/Midwest Technical Field Manager
817 793-4578